With its technology and process management, our facility in the Gördes district of Manisa, which is among the top 10 facilities in the world in its field, holds the distinction of being the first specialized enterprise established in Turkey to develop nickel-cobalt resources. Our facility consists of four main sections: "Nickel Open Pit Mine," "Limestone Quarry," "High-Pressure Leach Plant," and "Auxiliary Facilities."
Completed in Gördes with Zorlu Holding's entrepreneurial spirit and industrial identity, the production facility has a capacity of 10,000 tons of nickel metal, and with the second phase investment, the production capacity will reach 20,000 tons of nickel metal.
Our company, which started trial production in the last quarter of 2014 in Gördes with proven reserves of 300,000 tons (nickel metal content), began commercial production in 2015, completing its first export. In the upcoming period, through the development of technology and increased efficiency, the operational lifespan of the facility will be extended, enabling it to operate at an even higher capacity.
Our company, advancing its studies from mining to minerals with advanced material technologies, continues to work to transform nickel mining in Turkey into an innovative business area that creates high added value. As we complete the first phase of our investment in Gördes and transition to the operational period, we continue reserve development and ore production in Eskişehir, and geological survey studies in Uşak.
While our R&D studies in the field of scandium and rare earth elements continue, we also conduct evaluations of different earth elements, especially iron, in the areas where we have licenses.
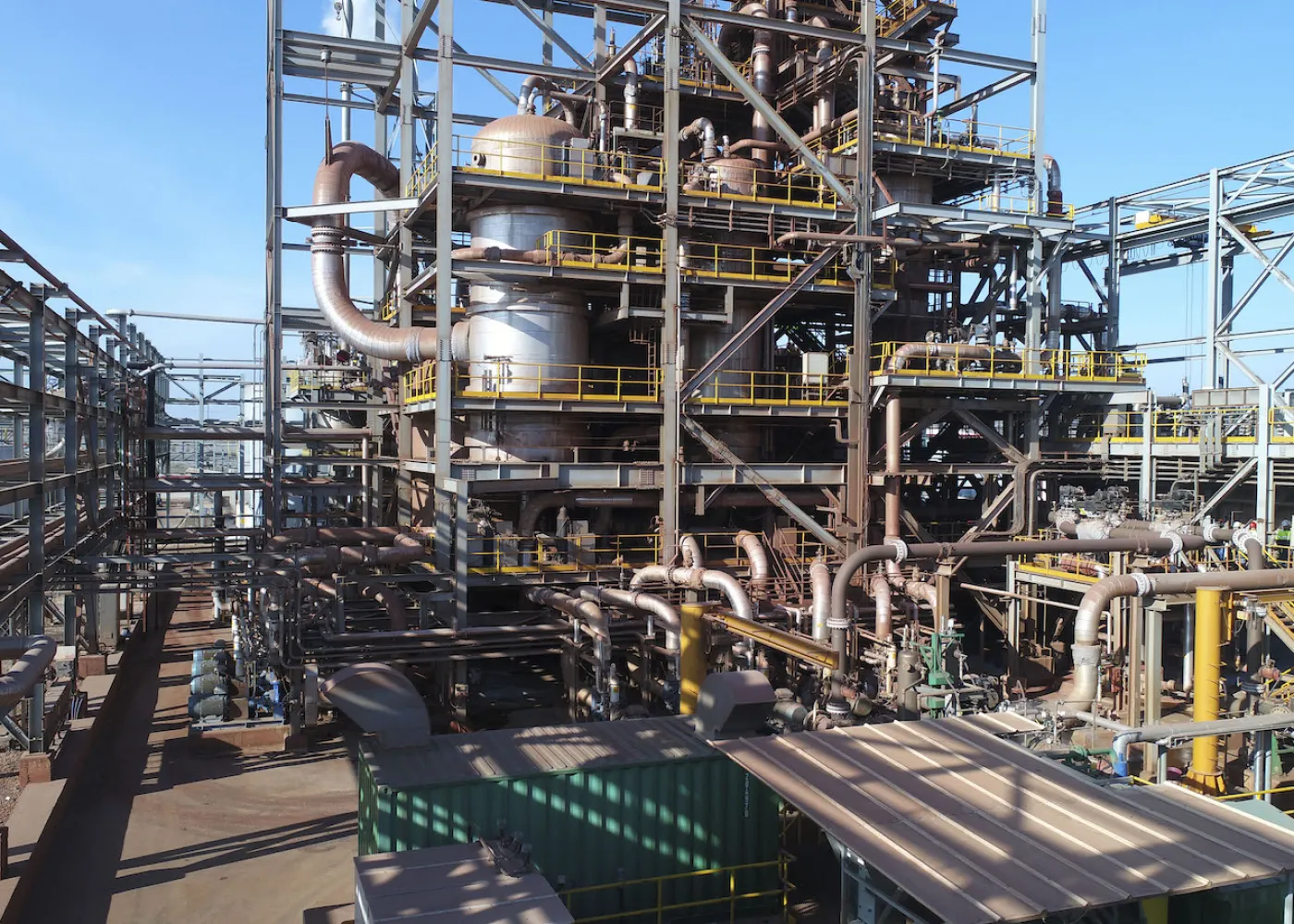
Following extensive research conducted on the licensed lateritic nickel ore fields of Meta Nikel Kobalt A.Ş's Gördes facility, it has been determined that the most efficient hydrometallurgical recovery method is the state-of-the-art High-Pressure Acid Leaching (HPAL) process. All investments have been directed towards this hydrometallurgical process. This facility, a rarity worldwide, stands as a source of pride in Turkey due to being the sole application of its kind.
The HPAL process is a cutting-edge technology applied for the selective dissolution of nickel and cobalt in a titanium alloy autoclave reactor under high pressure and temperature conditions (255°C and 46 bar). In this hydrometallurgical process, the slurry introduced into the high-pressure system is heated with steam recovered from expansion tanks in a gradual manner. It is then transferred to the autoclave reactor using specially designed pumps for this process, where it is dissolved with sulfuric acid. Due to the influence of temperature and high pressure, all reactions take place within a short period, approximately one hour, with high dissolution efficiency, and the autoclave reactor is then gradually depressurized and cooled in three stages in the expansion tanks, ultimately returning to atmospheric conditions.
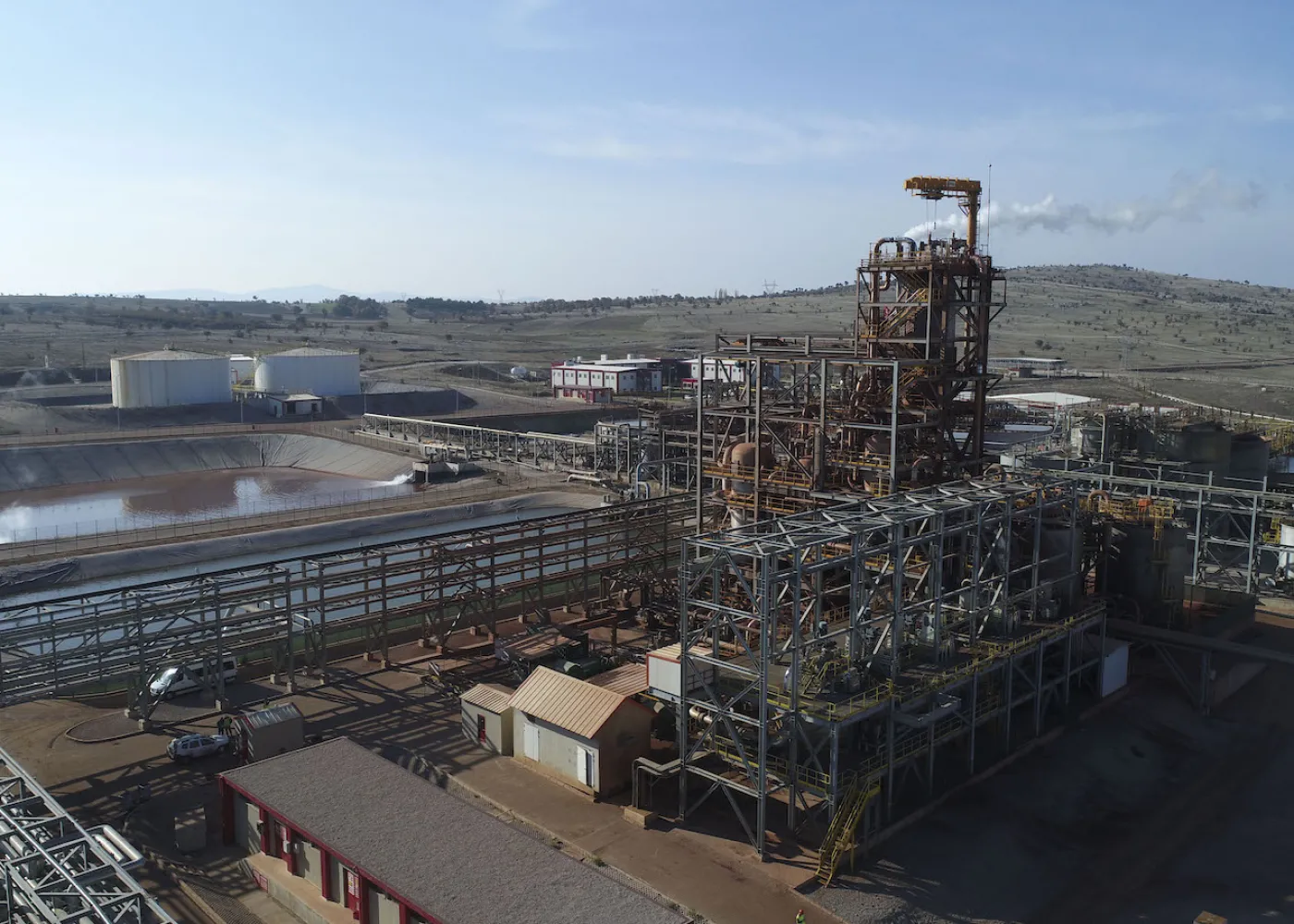